Introduction :
PROFINET stands for Process Field Net and PROFINET speed is 100 megabits per second up to 256 devices can be connected to a single PROFINET. Ethernet and information technology (IT) are gradually taking the lead in today’s automation technology because to well-known protocols as TCP/IP and XML . Integrating information technology into automation opens up significantly better communication options between automation systems, extensive configuration and diagnostic possibilities, and network-wide service functionality. These functions have been integral components of PROFINET from the outset. PROFINET is the open standard for industrial Ethernet, covering all the requirements of automation technology . Whether the application involves production automation, process automation or drives (with or without functional safety), PROFINET is the first choice across the board. This technology has become standard in the automotive industry, widely disseminated in machine building and well-proven in the food and packaging, logistics and process industries.
What is PROFINET:
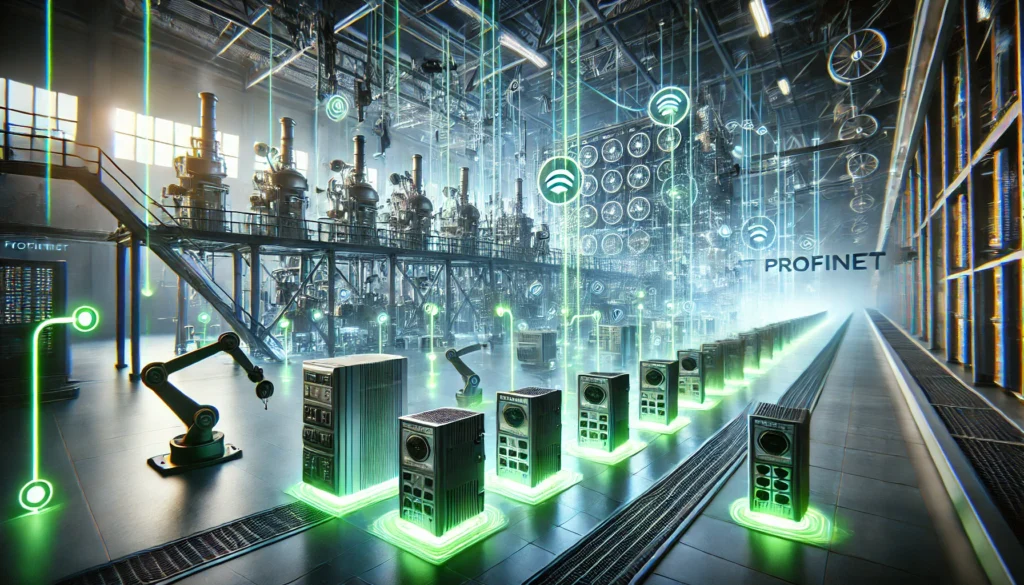
PROFINET stands for Process Field Net. PROFINET is an open Industrial Ethernet standard developed by the PROFIBUS Organization – PI.
- is completely standard Ethernet (IEEE802.3).
- operates at 100Mbit/s over twisted-pair copper or fibre- optic cables.
- makes use of TCP/IP and other IT standards for non-real- time communications (i.e. configuration and parameters).
- Provides a “real-time” channel for time-critical communications (i.e. process data)
PROFINET Features :
1)Ease of use : The user-friendliness of PROFINET minimizes the costs of installation, engineering and commissioning for machine and system builders. The system owner profits from ease of system expansion, high system availability and fast and efficient communication.
2)Flexible network topology : PROFINET is switched Ethernet. To make out cost-effective and easy, many PROFINET devices already have a switch with two or more ports integrated into them. PROFINET is 100% Ethernet compatible as per IEEE standards and full fills system requirements with its flexible topology. Line, ring and star structures are easy to implement with copper and fiber-optic cables. PROFINET enables wireless communication with WLAN and Bluetooth.
3)Integrated diagnostics : PROFINET includes intelligent diagnostic concepts for field devices and networks. A cyclically transmitted diagnostic data provides important information on the status of the devices and
communication and enables a user-friendly representation of the network.
4)Integrated safety: PROFISAFE the tried-and-tested technology for PROFIBUS functional safety, is also available for
PROFINET. The ability to use the same cable for standard and safety-related communication yields savings for devices, engineering and setup
5)High availability : PROFINET integrates automatically responding redundancy solutions. The defined concepts for
system redundancy and Dynamic Reconfiguration (DR) increase system availability considerably.
6)Scalable real time: Communication takes place over the same cable in all applications, from simple control tasks to
highly demanding motion control applications. For high-precision closed-loop control tasks, deterministic and isochronous transmission of time-critical process data with a jitter of less than 1µs is possible.
7)powerful system base: PROFINET fulfills the most wide-ranging requirements with its consistent, Ethernet-based
communication. From data-intensive parameter configuration to extremely fast IO data transmission, PROFINET enables automation in real time and IT integration with a single system. This is a basic requirement for Industrial 4.0
8)Support for energy optimization: With the PROFI energy profile integrated into PROFINET devices, the energy use in an automation system can be measured using a standardized method and controlled by selectively switching
functions on and off without additional hardware.
9)Sensor/actuator integration: IO-Link, the globally standardized IO technology (IEC 61131-9) for communicating with sensors and actuators, can be optimally integrated into PROFINET. This enables digital communication up
to the sensor/actuator level.
10)Global support: With its network of Competence Centers, the PROFIBUS & PROFINET International (PI) organization offers solid training and consultation across the globe. Establishment of the proven certification process achieves a high standard of quality for PROFINET products and their interoperability in systems.
How PROFINET Work:
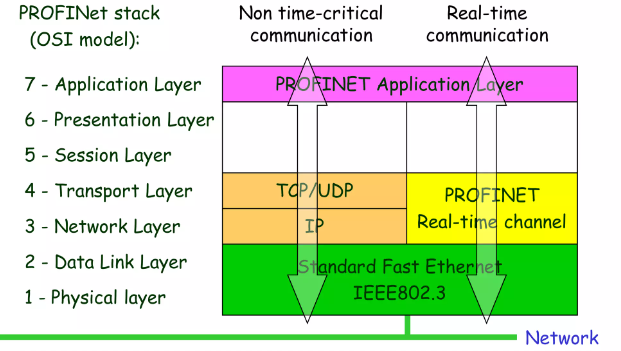
The TCP/IP channel is used for non-time critical tasks.
- Downloading of configuration, parameters.
- Diagnostics.
- Device management information, etc.
The Real-Time channel is used for time-critical data:
- Cyclic process data.
- Alarms and critical messages.
- Communication monitoring.
The PROFINET application layer protocol is defined in the International Fieldbus standard IEC61158 (type 10)
Physical Layer: PROFINET uses standard Ethernet (IEEE 802.3) technology, which is exactly how data is transmitted at the physical level.
Data Link Layer: PROFINET uses standard Ethernet framing (IEEE 802.3) for most communications, but it also introduces Real-Time (RT) and Isochronous Real-Time (IRT) protocols at this layer to prioritize time-sensitive industrial data. This is an enhancement to standard Ethernet, ensuring faster and deterministic data delivery.
Network Layer : PROFINET uses IP addressing at this layer, making it compatible with standard Ethernet and IT networks. This allows PROFINET devices to communicate in both industrial settings and traditional IT environments.
Transport Layer: PROFINET also uses TCP/IP or UDP for non-real-time communication (e.g., configuration, diagnostics). However, for time-critical data exchange, PROFINET avoids these general-purpose protocols to reduce latency, using specialized real-time communication mechanisms.
Session, Presentation, and Application Layers: In PROFINET, these layers are handled by various profiles and protocols. For example:
- PROFINET RT and IRT handle real-time communication at the application level.
- PROFIsafe ensures safety-related communications (such as emergency stops).
- PROFIenergy is used for managing energy consumption.
PROFINET combines some of these layers into a more practical industrial solution for real-time and deterministic data exchange.
Learn About OSI LAYERS : CLICK HERE
PROFINET Conformance Classes:
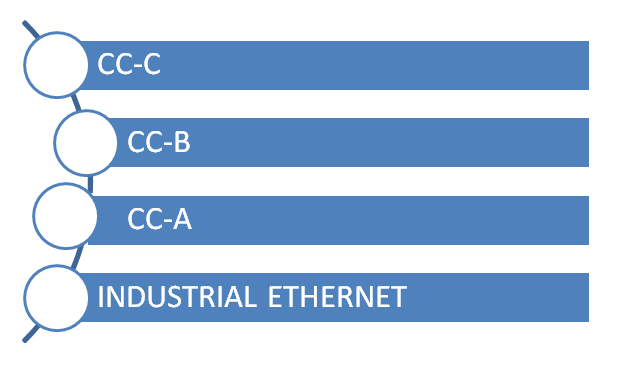
There are three Conformance Classes (CC) which build upon one another (see Figure)
Conformance Class A (CC-A) provides basic functions for PROFINET with real-time (RT) communication. All IT services can be used without restriction. Typical applications are found, for example, in business automation. Wireless communication is specified for this class.
Conformance Class B (CC-B) expands PROFINET to include network diagnostics using IT mechanisms and topology information of the network.
Conformance Class C (CC-C) describes the basic functions for devices with hardware-supported bandwidth reservation and synchronization Isochronous Real-Time (IRT) communication and is thus the basis for isochronous applications.
Advantage PROFINET :

- Able to operate in harsh industrial environment
- Able to deliver the required speed and precision
- Highly scalable architectures.
- Access to field devices over the network.
- Maintenance and servicing from anywhere (even over the internet).
- Lower costs for production/quality data monitoring.
- Can provide Safety, Energy Management and IT Integration
PROFINET IO:
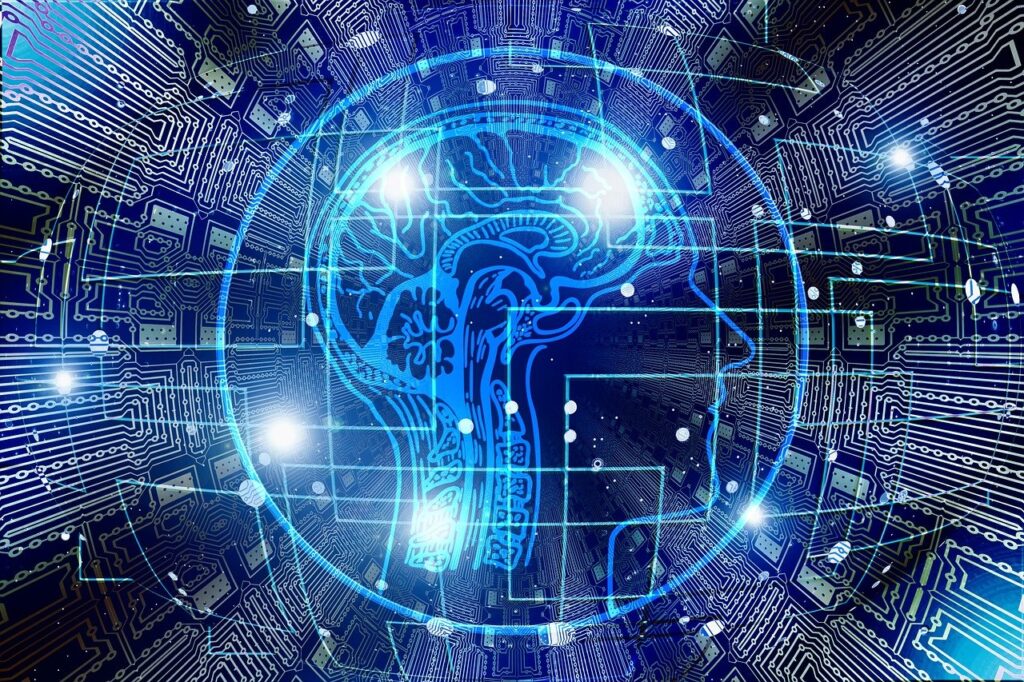
PROFINET IO provides decentralized peripherals using Ethernet connection and the PROFINET communication protocol. PROFINET IO uses Real-Time and Non Real-Time communications. PROFINET makes use of relevant TCP/IP protocols for setup, configuration and maintenance functions:
- DHCP – Dynamic Host Configuration Protocol,
- DNS – Domain Name Service,
- SNMP – Simple Network Management Protocol,
- ARP Address Resolution Protocol,
- HTTP – Hyper Text Transfer Protocol.
IO controller: This is typically the Programmable Logic Controller (PLC) in which the automation program runs. The IO controller provides output data to the configured IO devices in its role as provider and is the consumer of input data.
IO device: An IO device is a distributed IO field device connected to one or more IO controllers via PROFINET. The IO device is the provider of input data and the consumer of output data from the IO controller.
IO supervisor: This can be a programming device (PG), personal computer (PC) or human machine
interface (HMI) device for commissioning or diagnostic purposes.
Device Descriptions(GSDML):

To enable system engineering, the GSD files (General Station Description) of the field devices to be configured are required. This XML-based GSD describes the properties and functions of the PROFINET field device, including its modules and submodules. It contains all data relevant for engineering as well as for data exchange with the field device.
In particular, GSD files enable the engineering of a PROFINET system or PROFINET application without the devices used having to be physically present.
The GSD is essential for a PROFINET field device, as engineering is impossible without it. Every manufacturer of a PROFINET field device must create an associated GSD file. It will be checked as part of the certification test
PROFINET Security :
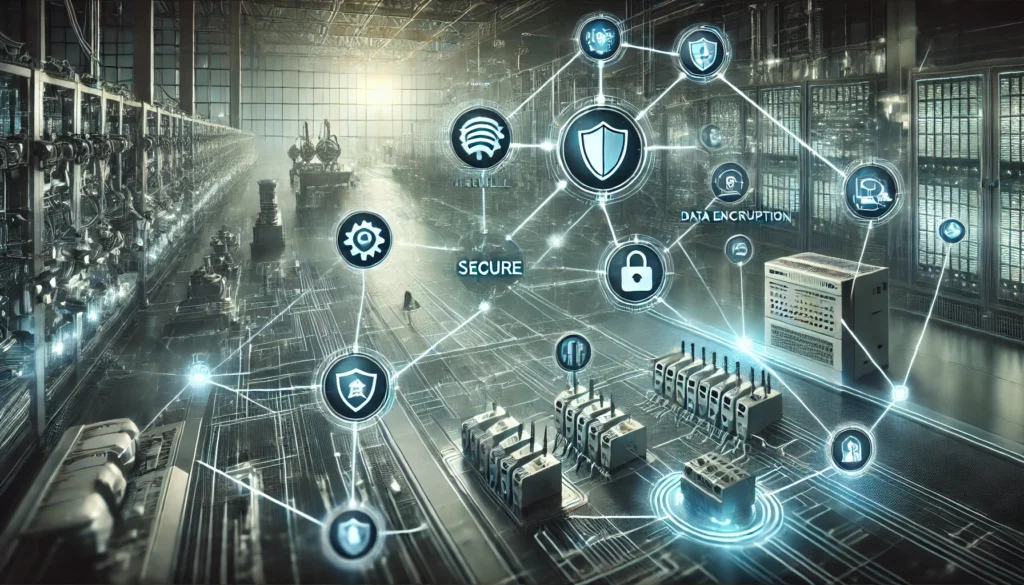
For networking within a larger production facility or over the Internet, PROFINET relies on a layered security concept. This recommends a security concept optimized for the specific application case, with one or more upstream security zones. On the one hand, this unburdens the PROFINET devices, and on the other, it allows the security concept to be optimized to changing security requirements in a consistent automation engineering solution. The security concept provides for the protection of both individual devices as well as whole networks from unauthorized access. In addition, there are security modules that will allow networks to be segmented and thus also separated and protected
from a safety standpoint.
PROFIsafe:
The PROFIsafe designation refers to the protocol defined in IEC61784-3-3 for the implementation of functional safety (fail-safe) and is recognized by IFA and TÜV. PROFIsafe can be used with PROFIBUS and PROFINET alike. Fail-safe (F) is the ability to reliably protect a system from hazards or to reduce the risk to an acceptable level with corresponding technical and organizational measures. The use of PROFIsafe enables elements of a fail-safe controller to be transferred directly to standard.
PROFIenergy:
The high cost of energy and compliance with legal obligations are compelling the industry to engage in energy conservation. Recent trends toward the use of efficient drives and optimized production processes have been accompanied by significant energy savings. However, in today’s systems and production units, it is common for numerous energy consuming loads to continue running during pauses.
PROFIenergy enables active and effective energy management. By purposefully switching off unneeded consumers, energy demand and thus energy costs can be significantly reduced. PROFINET nodes in which PROFIenergy functionality is implemented can use the commands to react flexibly to idle times. In this way, individual devices or
unneeded portions of a machine can be shut down during short pauses, while a whole system can be shut down in an orderly manner during long pauses. Using PROFIenergy, it is also possible to measure and optimize the energy consumption of production
Cables for PROFINET:

The maximum segment length for electrical data transmission with copper cables between two nodes (field devices or switches) is 100 m. The copper cables are implemented uniformly in AWG The installation guideline defines different cable types that have been optimally adapted to their respective industrial applications. Sufficient system
reserves allows installations that are suitable for industrial use with no limitation on transmission distance
PROFINET type A: Standard permanently-routed cable, no movement after installation.
PROFINET type B: Standard flexible cable, occasional movement or vibration.
PROFINET type C: Special applications: Highly flexible, constant movement (tow-chain or torsion,
for example)
PROFINET type R: Robot applications, tested specifically for this application. for data exchange with the field device.