Introduction
PLC (Programmable Logic Controller) and SCADA (Supervisory control and data acquisition) are the two widely used systems in an industrial automation environment. Both are used to automate processes, but they are not identical. PLCs as due controls the machinery and processes SCADA, on an interface for more centralized control platform of many systems.
In the following article, we will explain the main differences between PLC and SCADA in order to help you determine when to apply technology or not.
What is a PLC?
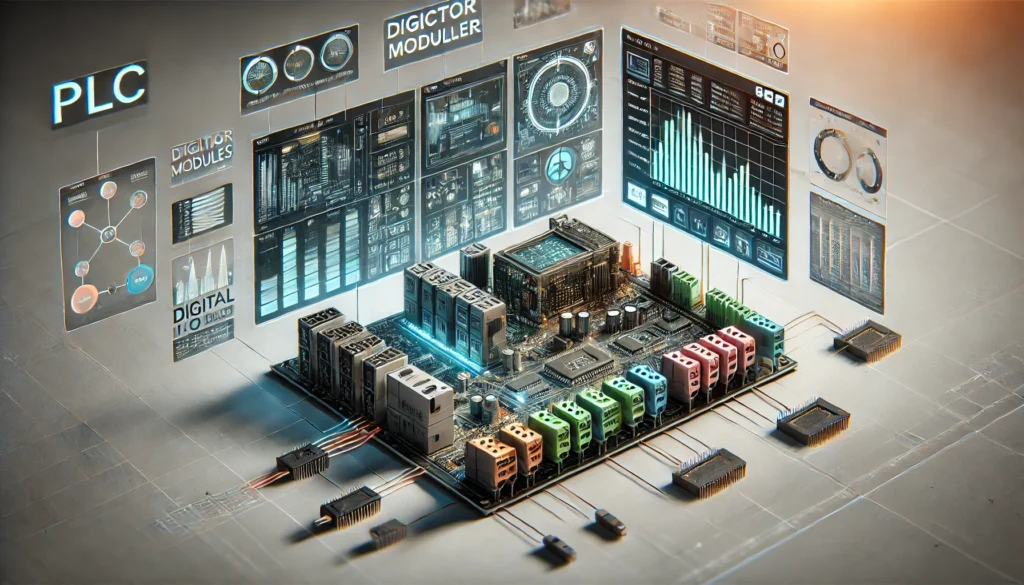
Definition and Functions
A PLC (Programmable Logic Controller) is a digital computer used for automation of electromechanical processes, such as control of machinery, factory assembly lines, and other industrial equipment. Usually, PLCs are designed for use in manufacture plants, assembly lines and other automated production processes.
History of PLCs
The prototype PLC designed by Dick Morley for General Motors is considered to be the first ever PLC and it came about in the final 1960s. In the early days, heavy and thinking was based on relay logic circuits for industrial machinery where PLCs are very thick and complex to change, maintaining, fails quickly. The PLCs (Programmable Logic Controllers) emerged as a reliable and flexible alternative, transforming the field of industry automation.
Components of a PLC
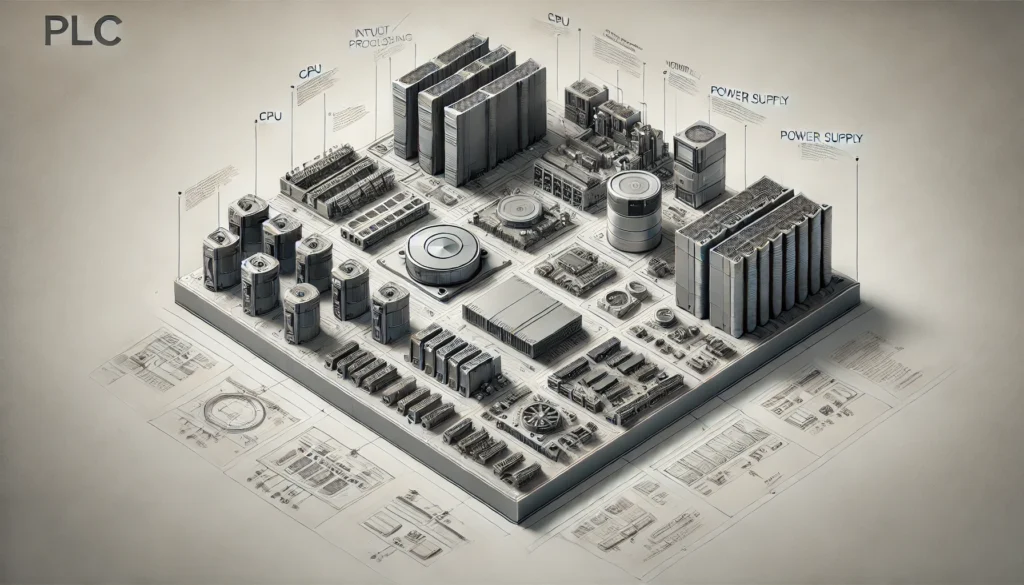
CPU (Central Processing Unit): The PLC’s “brain,” which processes logic, runs programs and communicates with external devices.
Input/Output (I/O) Modules : Interfaces that allow the PLC to read data from sensors (inputs) and to output control signals to actuators
Power Source: Supplies power for the PLC and some of its components.
Programming Device: The device to use for writing and downloading programs into the PLC — either a computer or a handheld gadget.
Communication Ports: Interfaces for communication between PLC and other systems (SCADA, other controllers)
How PLC Works
At its core, a PLC works based on logic- instructions written or programmed into it. The inputs are constantly scanned then the logical operations take place in CPU and it updates its actuation with respect to program logic output. The program is then typically written in such languages as Ladder Logic, Function Block Diagram (FBD), or Structured Text (ST).
What is SCADA?
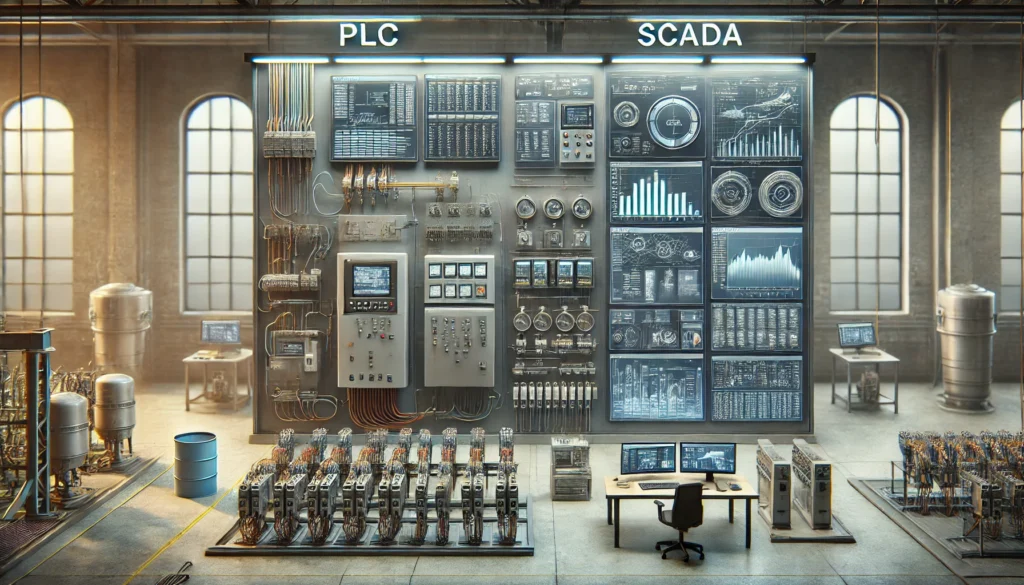
Definition and Functions
SCADA (Supervisory Control and Data Acquisition) is a class of software application program for process control. SCADA is used to acquire real-time data from remote locations and further offers a human interface for operators to monitor, control and analyze processes.
History of SCADA Systems
Emerging in the 1960s and 70s, SCADA systems were designed to receive data on industrial processes via telemetry with a goal of central control. With advances in networking, communication technologies, and computing power these have significantly evolved.
Components of SCADA
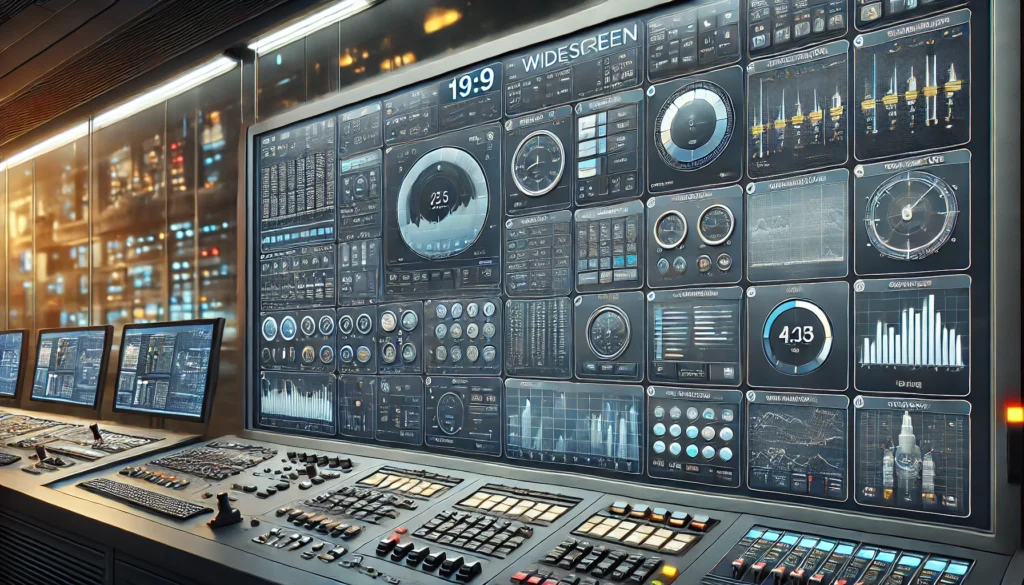
Human-Machine Interface (HMI): A graphical user interface that allows operators to interact with the system, monitor processes, and control equipment.
Data acquisition: This takes data from field devices: PLC, RTU, and sensors.
Central Supervisory System: Central system which supervises the whole process —usually a server or set of servers.
Remote terminal units (RTUs): These machines connect to field sensors and equipment, sending data back to the central SCADA system.
Communication infrastructure: A vast system of communication channels — wired, radio or satellite technologies connected to the field devices that communicate with a supervisory system.
How SCADA Works
Data from field devices are collected via SCADA systems and sent to the central system. The HMI allows operators to view and analyze this data in real-time. The SCADA system sends control commands to PLCs or RTUs, adjusting set points and manually overriding operations if necessary.
Key Differences Between PLC and SCADA
PLC | SCADA |
Designed for direct control of machinery and processes. | Primarily used for monitoring, supervisory control, and data acquisition from multiple devices, including PLCs. |
Consists of physical hardware like CPUs, I/O modules, and power supplies. It is programmed with software tools such as Ladder Logic or Structured Text. | A combination of hardware (RTUs, sensors) and software (HMI, data acquisition). SCADA systems typically run on centralized servers or workstations. |
Communicates directly with field devices and controls processes in real time. | Communicates with multiple devices (including PLCs) to gather data and provide high-level control. |
Processes real-time data and executes control logic. | Focuses on data acquisition, monitoring, and providing reports, trends, and analytics to operators. |
Best suited for small to medium-sized automation tasks. | Designed for large-scale systems that require supervisory control of multiple processes spread across vast distances. |
Integration of PLC and SCADA
How They Work Together
PLC and SCADA implement this seamless control together in many industrial automation systems. PLC controls the local machinery, and SCADA gives a central interface to monitor and supervisor control over an entire plant or network of sites.
Advantages of PLC
Reliability: PLCs are durable and built for industrial environments.
Control in Real-time: Because PLCs are faster than a standard PC the processing of information is measured in microseconds so you get near instant control of the machinery as soon as new information comes to light.
Variable: Simple to reprogram and change for various undertakings.
Advantages of SCADA
Centralized monitoring : SCADA is suitable for large-scale operations as it allows for a bird’s eye view of industrial processes
Using SCADA Systems for Data Analysis:-SCADA offers robust trending, reporting and analytical tools for historical data analysis.
Remote Access: Remote monitoring and control of processes by the operator.
Applications of PLC and SCADA
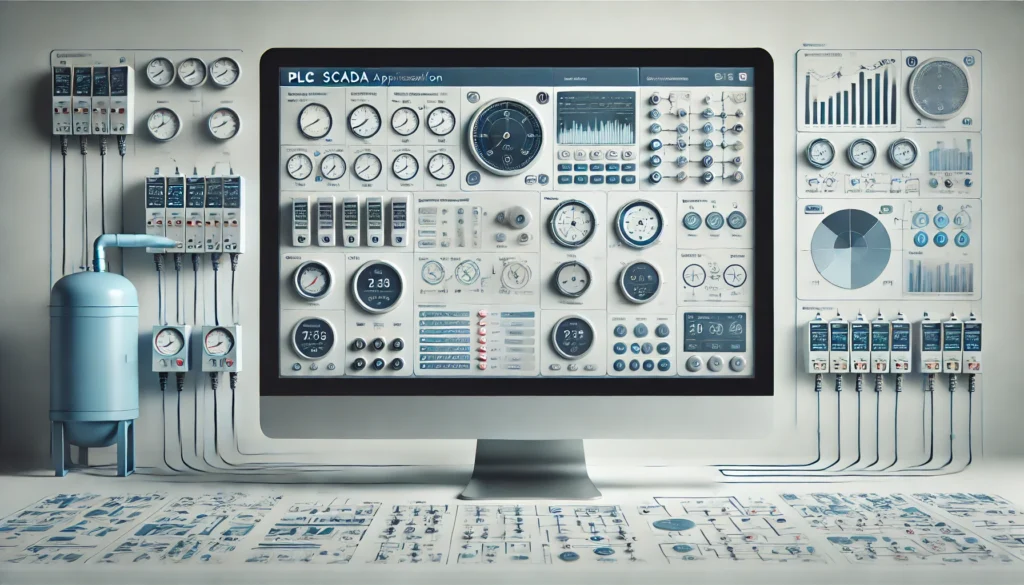
PLC Applications:
- Assembly line
- control Packaging
- machines Motor
- pump control
SCADA Applications:
- Water treatment plants
- Power generation and distribution
- Oil and gas pipelines
Conclusion
PLC and SCADA have become the backbone of any industry. PLCs allow control of machinery and processes in real-time, whereas SCADA systems give its operators a higher level overview to monitor, analyze, and possibly control large-scale operations. By properly analyzing these technologies, industries can fine-tune their automation strategies to enhance productivity, efficiency and safety.
The integration of PLC and SCADA systems allows industries to have the best of both worlds — granular control over machines as well as high-level supervision, thereby ensuring a smooth flow of operation.
Nice informative