Introduction:
A Variable Frequency Drive (VFD) controls the speed of a motor, specifically a three phase motor. To better understand a VFD, let’s examine the motors they control. Most commercial HVAC systems require powerful motors, and often operate on a three phase power (The standard method for electric power distribution systems because of its efficiency). A three phase motor is cheaper to operate than single phase motors because it uses less current (less current often results in reduced wire size and cost), especially where large motor requirements are necessary. A VFD eliminates high in-rush current – When a standard motor is turned on, it draws a very high amount of current for a very short duration of time. A Variable Frequency Drive is designed to slowly start, therefore preventing inrush current; reducing the stress on the components of the motor; thus extending the motor life. A VFD controls the speed of a three phase AC motor, while resulting in energy savings! It saves energy because the motor does not require as much current at lower speeds. The solution is a Variable Frequency Drive (VFD)
what is a VFD :
A variable speed drive converts the electrical power supply from fixed voltage and fixed frequency to a variable voltage and frequency making it possible to adjust the speed of a standard electrical motor. A Variable Frequency Drive (VFD) is used to control the speed of the induction motor, through changing the input frequency and voltage. It varies both the frequency and amps of the AC waveform being delivered to the motor saving money in electricity.
The need of VFD :
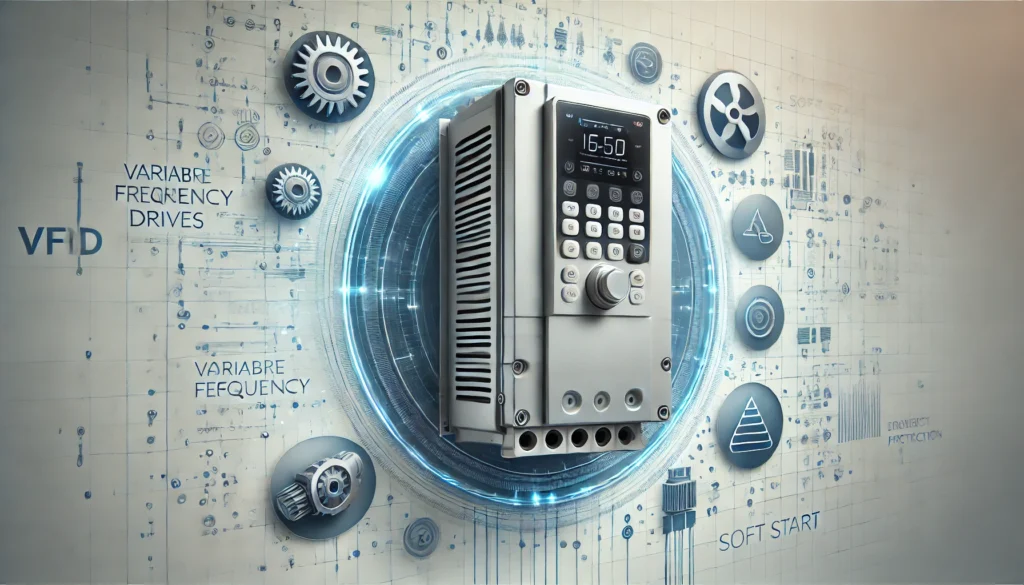
There are many and diverse reasons for using variable speed drives such as :
- pump and fan applications.
- control and regulation.
- Speeding up or slowing down a machine or process.
- Protection from overload currents
- Protection from short circuit.
- Protection from phase loss.
- Safe Acceleration
The needs for speed and torque control are usually fairly obvious. Modern electrical VFD can be used to accurately maintain the speed of a driven machine to within ±0.1%, independent of load, compared to the speed regulation possible with a conventional fixed speed squirrel cage induction motor, where the speed can vary by as much as 3% from no load to full load. The benefits of energy savings are not always fully appreciated by many users. These savings are particularly apparent with centrifugal pumps and fans, where load torque increases as the square of the speed and power consumption as the cube of the speed. Substantial cost savings can be achieved in some applications.
How Does a VFD Work?

Rectifier: Converts AC power into direct current (DC).
DC Bus: Stores and smooths the DC power, often with capacitors or filters.
Inverter: Converts DC power back into AC with variable frequency and voltage.
Variable AC Output: The adjustable AC output is sent to the motor, controlling its speed and torque.
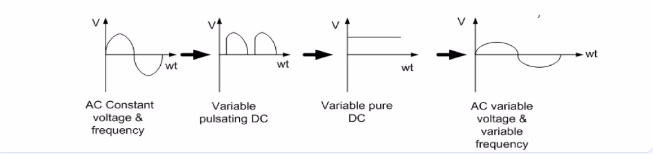
Let’s break a VFD into its three primary stages to better understand how it operates:
- Rectification: The input AC power (from the power grid) is first transformed into DC (Direct Current) power by the VFD. This is accomplished by converting the alternating current into a direct current, a process known as rectification.
- DC Bus: The rectified DC power is then stored in the VFD’s DC bus. This stage smooths the current and prepares it for the next step.
- Inversion: Lastly, an inverter circuit transforms the DC power back into a variable AC output, modifying the voltage and frequency that are sent to the motor.
Benefits to use VFD :
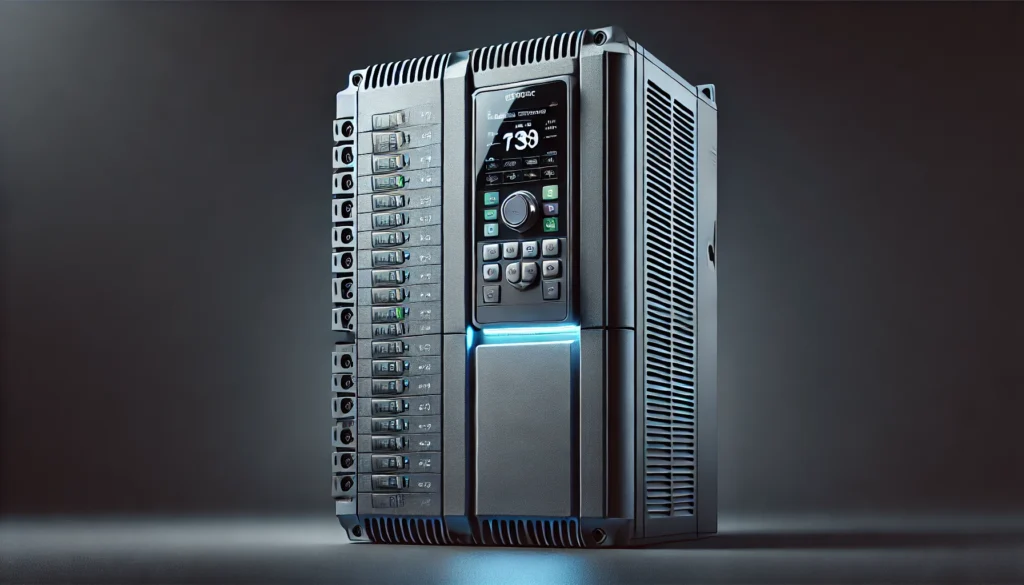
- Saves energy – “excess capacity” of systems
- Better regulation and control of the Process
- Reduces overall equipment and installation costs
- Reduces maintenance costs due to smooth start.
- Reduces installation costs.
- Reliable Start/Stop & Synchronization
- Reduction in Maximum Demand
- Starting Current restricted to 100% of full load current.
- Improved Power Factor.
- Huge Energy Saving with Nominal Speed Control
- Provides the most efficient means of motor speed control.
- Reduces the thermal and mechanical stresses on the motor
- Improved efficiency of motor.
- VFD also have communication interface.
Drawbacks VFD:
- Initial cost of installing VFDs can be expensive.
- VFDs can produce harmonic distortion.
- Special shielded cable is used .
- Separate arrangement is required for VFD
Application VFD:
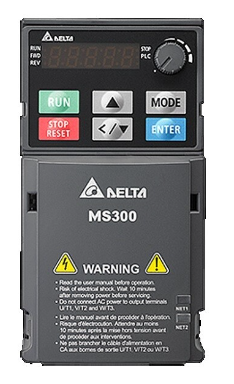
- Conveyor Systems.
- CNC machine
- Industrial automation system
- Pumps
- Fans and Blowers
- Centrifugal Pumps and Compressors
- Cranes and Hoists
- Extruders
- Mixers and Agitators
- Elevators and Escalators
- Textile Machinery
- Compressors (Refrigeration and Air Conditioning)
- Mining and Quarrying
- Oil and Gas Industry
- Agriculture
- Renewable Energy (Wind Turbines and Solar Pumps).
- Marine Industry
Types of VFD :
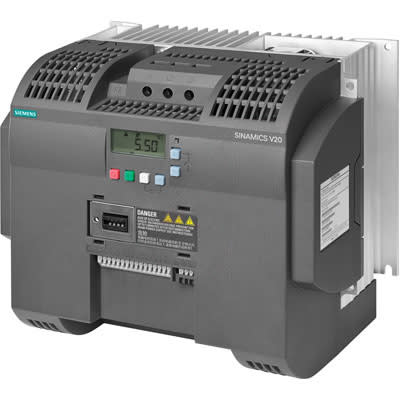
- Voltage Source Inverter (VSI) VFD
- Current Source Inverter (CSI) VFD
- Pulse Width Modulation (PWM) VFD
- Direct Torque Control (DTC) VFD
- Cycloconverter VFD
- Harmonic Neutralized PWM VFD
- Scalar Control VFD (V/f Control)
- Vector Control VFD (Field-Oriented Control)
- Servo Drives (for VFD-controlled Servo Motors)
- Multi-Level VFD
Functions & Features VFD:
- Set-up Parameters
- The Control Method
- Acceleration or Accel-Ramp Rate
- Automatic Restart
- Stopping Method
- Automatic Signals
- Fault Diagnostics and Alarming
- Safety Functions
- Motor Protection Features
- Feedback Control
- Programmable Logic Control (PLC) Integration