Introduction:
- Actuators extract energy from fluid, pneumatic or electric, and convert it to mechanical energy to perform useful work.
- Linear actuators –Cylinders
- Rotary actuators –Motors
What Is Actuator :
In industrial control systems, an actuator is a hardware device that converts a controller command signal into a change in a physical parameter. The change in the physical parameter is usually mechanical, such as a position or velocity change. An actuator is a transducer, because it changes one type of physical quantity, such as electric current, into another type of physical quantity, such as rotational speed of an electric motor. The controller command signal is usually low level, and so an actuator may also require an amplifier to strengthen the signal sufficiently to drive the actuator.

Actuator Category:
Most actuators can be classified into one of three categories, according to the type of amplifier: (1) electric, (2) hydraulic, and (3) pneumatic.
1) Electric actuators are most common; they include electric motors of various kinds, solenoids, and electromechanical relays. Electric actuators can be either linear (output is linear displacement) or rotational (output is angular displacement).
2) Hydraulic actuators use hydraulic fluid to amplify the controller command signal. The available devices provide either linear or rotational motion. Hydraulic actuators are often specified when large forces are required.
3) Pneumatic actuators use compressed air (typically “shop air” in the factory) as the driving power.
Again, both linear and rotational pneumatic actuators are available. Because of the relatively low air pressures involved, these actuators are usually limited to relatively low-force applications compared with hydraulic actuators.
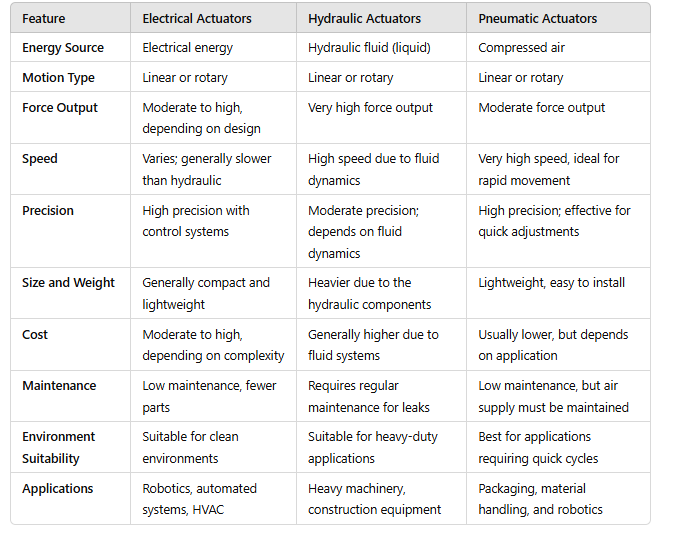
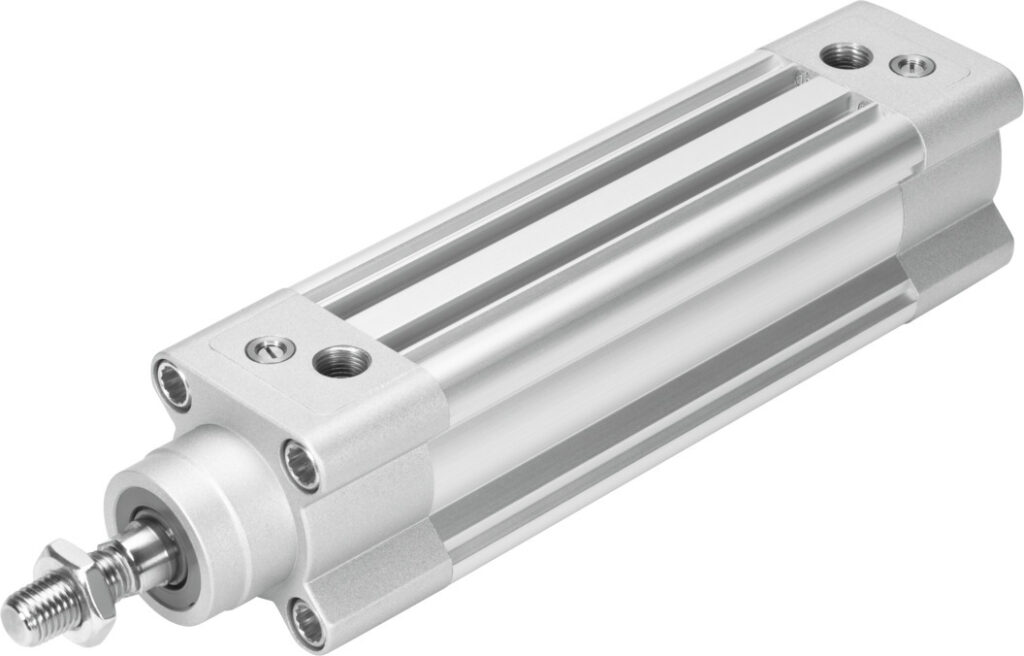
Actuator Types:
Rotary actuator: A rotary actuator is an actuator that produces a rotary motion or torque. An actuator that directs force in a circular motion. Rotary actuators are sometimes called motors. A rotary actuator is the most compact device available for producing torque from hydraulic or pneumatic pressure.
Linear Actuators: Linear Actuators are Actuators that creates motion in a straight line, as contrasted with circular motion of a conventional electric motor. Linear actuators are used in machine tools and industrial machinery, in computer peripherals such as disk drives and printers, in valves and dampers, and in many other places where linear motion is required. Hydraulic Cylinders or Pneumatic Cylinders inherently produce linear motion; many other mechanisms are used to provide a linear motion from a rotating motor.
Smart Actuators: These are integrated with sensors and communication capabilities, allowing for more precise control and feedback in automated systems.
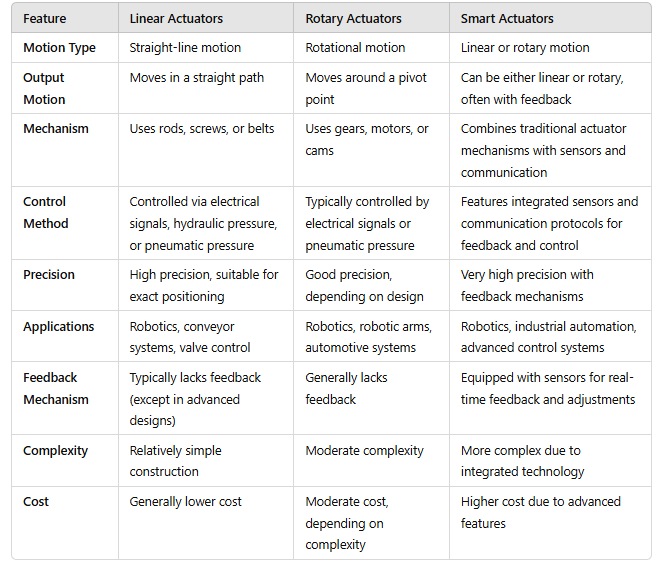
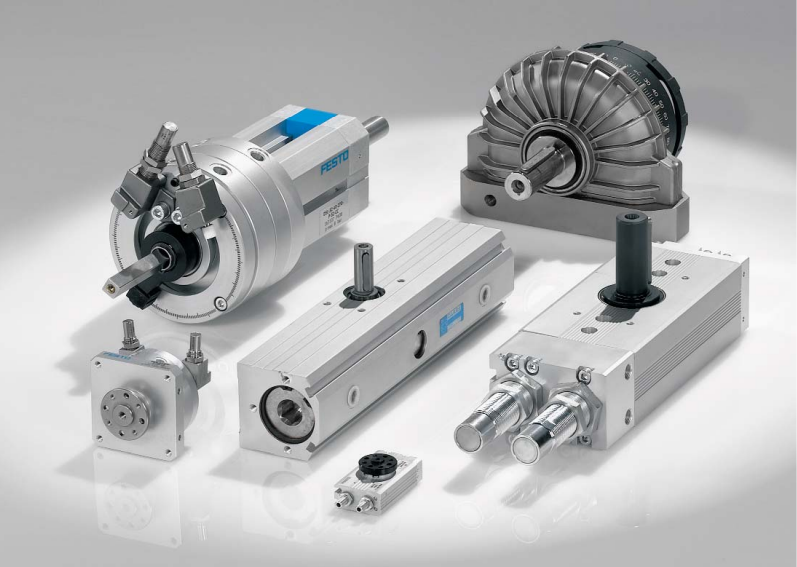
Applications of Actuators:
Actuator are mostly used in industrial automation and commercial applications.
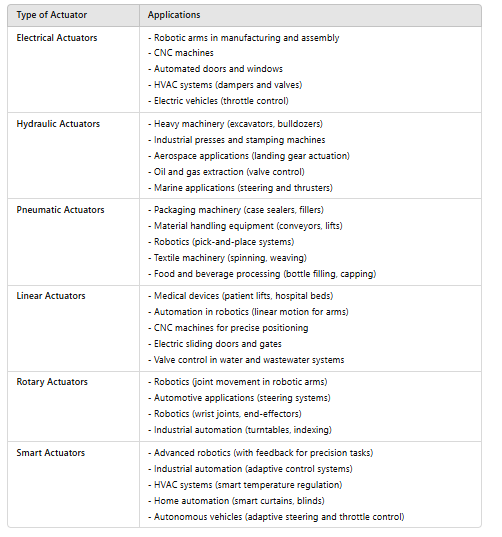
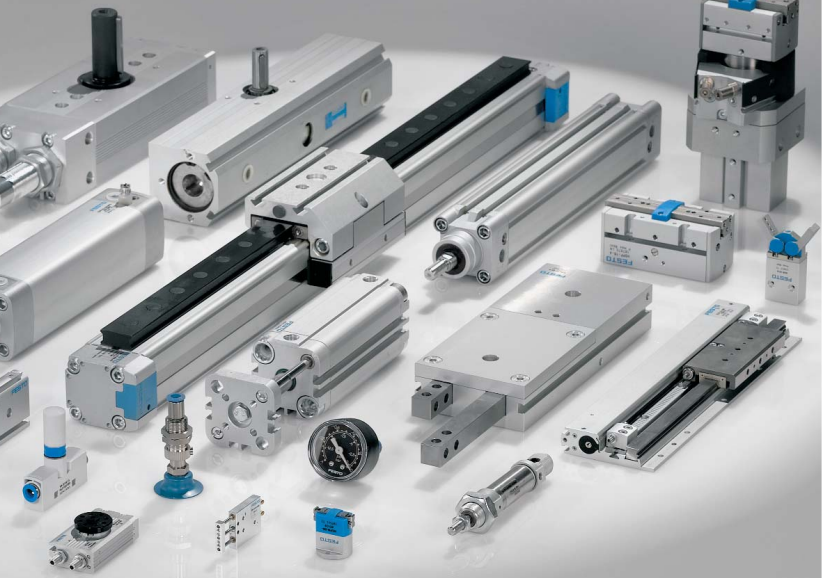
How to Chose Actuator:
Motion Type: Based on the needs of your application, decide if you want rotational (rotary) motion or straight-line (linear) motion.
Power Source: Choose between an electrical, hydraulic, or pneumatic power source.
Needs for Force and Load: Determine how much force is needed to complete the task. Make sure the chosen actuator can manage the anticipated load because different actuators have different force capacities.
Stroke Length and Speed: Determine how fast the actuator must travel. The speeds offered by various actuator types differ. Stroke Length: To guarantee that linear actuators can achieve the intended range of motion, provide the necessary stroke length.
Accuracy and Precision: Think of actuators with feedback mechanisms (such as smart actuators) that can give precise placement if your application requires a high level of accuracy.
Environment: Take into account the operational surroundings. Actuator lifetime and performance can be impacted by variables such as temperature, humidity, dust, and chemical exposure. Choose an actuator with the proper protection qualities (IP ratings, for example).
Compatibility of Control Systems: Make that the actuator is simple to incorporate into your current control system (SCADA, HMI, or PLC). Verify the control techniques (analog, digital, or fieldbus) and communication protocols.
Weight and Size Limitations: Examine the actuator’s physical space requirements. Take into account the weight and dimensions to make sure it satisfies your system’s design requirements.