History Of Robot:
- History Robot comes from the Czech word “robota”, that means tireless work.
When did robots, as we know them today, come into existence?
- 1)The first modern industrial robots, called Unimates, were developed by George Devol and Joe Engelberger in the late 50’s and early 60’s.
- 2)The first robot patents were by Devol for parts- transfer machines.
- 3) Engelberger formed Unimation and was the first to market robots. As a result, Engelberger has been called the ‘father of robotics.’
Progressive Advancement in Robots:
- First Generation (repeating, nonservo, pick and place, or point to point kind), in present 80% robots are of this kind.
- 1960 Second Generation (addition of sensing devices, path control capabilities).
- 1980 Third Generation (On-line computations and control, artificial vision, and active force/torque interaction with the environment).
- 1992 Fourth Generation (true android or an artificial biological robot or a super humanoid capable of its own clones). 2000
Industrial Robot Defination :
An industrial robot is a reprogrammable, multifunctional manipulator designed to move materials, parts, tools, or special devices through variable programmed motions for
the performance of a variety of tasks by. by Robotics Industries Association ( formerly Robotics Institute of America)
A machine capable of carrying out a complex series of actions automatically, programmable, that is to say, a machine resembling a human being and able to replicate certain human movements and functions automatically .A robot consists of ? electric, electronic and mechanical. The Robots are very good for certain functions, because unlike humans never get tired, or fatigued and can work in dangerous conditions, without air and without the easily distracted.
Industrial Robot Components:
Robot arms: Robots arms can vary in size and shape. The robot arm is the part that permit that the robot can move freely. With the robot arm, the shoulder, elbow and wrist move and twist to the exact position. A simple robot with three degrees of freedom can move in three ways: up & down, left & right, and forward & backward.
The end part(End effector): The end part connects to the robot’s arm tool and functions as a fingers of a hand. This part comes in direct contact with the material the robot is manipulating. Some variations of an effector are a gripper, a vacuum pump, magnets, and welding torches.
Sensors: Sensors allow the robot to receive feedback about its environment. The sensor collects information and sends it to the robot controlled. One use of these sensors is to keep two robots that work closely together from bumping into each other. Sensors can also assist end parts by adjusting for part variances. Vision sensors allow a robot to differentiate between items to choose and items to ignore.
The controller: The controller is the “brain” of the robot and allows the parts of the robot to operate together. The controller gives instructions written in code called a program.
The drive: The drive is the engine that moves the articulations into their designated positions. The joints are the sections between the parts of the robot. The following types of units are: hydraulic, electric, or pneumatic.
- Hydraulic drive systems give a robot great speed and strength.
- Electric system provides a robot with less speed and strength. Most read
- Pneumatic drive systems are used for smaller robots that have fewer axes of movement.
Industrial Robot Types:
Cartesian Robot
A type of robotic arm that has prismatic joints only. The linear movement of the joints gives the Cartesian robot a highly rigid structure that allows it to lift heavy objects.
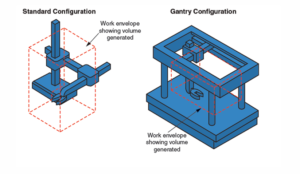
Cylindrical Robots :
Used for assembly operations, handling at machine tools, spot welding, and handling at die- casting machines. It’s a robot whose axes form a cylindrical coordinate system.
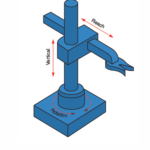
Spherical Robots:
Used for handling at machine tools, spot welding, die-casting, fettling machines, gas welding and arc welding. It’s a robot whose axes form a polar coordinate system.
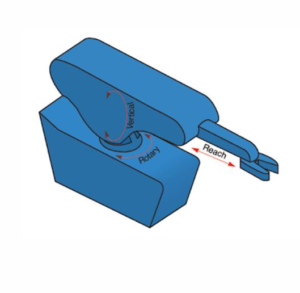
Scara Robot:
Used for pick and place work, application of sealant, assembly operations and handling machine tools. It’s a robot which has two parallel rotary joints to provide compliance in a plane.
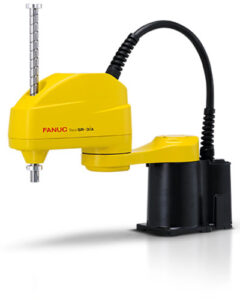
Articulated Robot :
Used for assembly operations, die- casting, fettling machines, gas welding, arc welding and spray painting. It’s a robot whose arm has at least three rotary joints
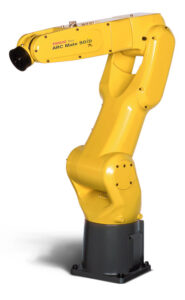
Parallel Robot:
One use is a mobile platform handling cockpit flight simulators. It’s a robot whose arms have concurrent prismatic or rotary joints.
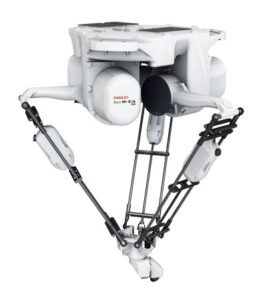
Industrial Robot Motion Control Method:
- The point-to-point system records a series of locations during the programming function and the robot moves to these points when the robot is in run mode.
- The continuous-path control is used where the robot must follow an exact path such as in welding or spray painting. Each location in the path is recorded when the robot is in teach mode, and then the robot will follow each path during playback or run mode.
- The XYZ control uses mathematical coordinates to determine each point in the program. All points in the program are identified by their X, Y, and Z coordinates and these points can be entered manually into the program or by moving the robot to the location and recording the location through a teach pendant.
- The positive-stop control is used primarily with pneumatic robots where an air cylinder is extended or retracted until it reaches a stop. The robot motion is determined by a sequencer/ logic controller that energizes each cylinder at the appropriate time. The positions for this robot program are determined
by the placement of each stop.
Industrial Robot Application:
- Material Handling/Palletizing
- Machine Loading/Unloading
- Arc/Spot Welding
- Water jet/Laser cutting
- Spray Coating
- Gluing/Sealing
- Investment casting
- Assembly
- Inspection
The Advantages of Industrial Robots
1)Robots can do some things more efficiently and quicker than humans.
2)Robots never get sick or need to rest, so they can work 24 hours a day, 7 days a week.
3)Greater output per hour with consistent quality.
4)Continuous precision in repetitive operation.
How to Choose the Right Industrial Robot:
- Robot Specifications
- Number of Axes
- Major axes, (1-3) => Position the wrist
- Minor axes, (4-6) => Orient the tool
- Redundant, (7-n) => reaching around obstacles, avoiding undesirable configuration
- Payload (load capacity).
- Repeatability.
- Precision and accuracy.
- Maximum speed.
Industrial Robot Manufactures:
- ABB Robotics
- FANUC.
- KUKA Robotics.
- Yaskawa Electric Corporation.
- EPSON Robots.
- DENSO Robotics.
- Kawasaki Robotics.
- Mitsubishi Electric.
- Hyundai Robotics.
- Nachi-Fujikoshi.
- Techman Robot.
Also Read :
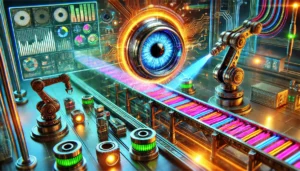
Introduction To Machine Vision | A guide to automating process & quality improvements
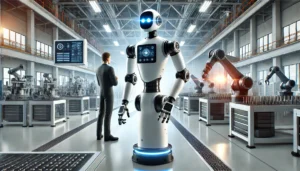
“What is a Cobot? A Beginner’s Guide to Collaborative Robotics”
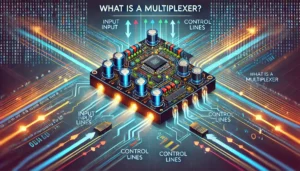
What Is A Multiplexer-Multiplexer Explained: Function, Types, and Real-World Applications
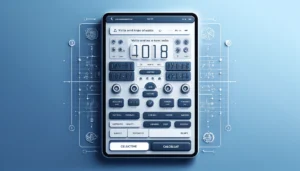
Amps to Watts Converter- Volts And Amps to Watts Converter
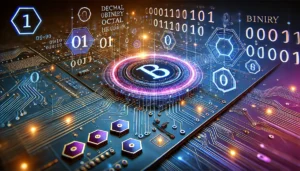
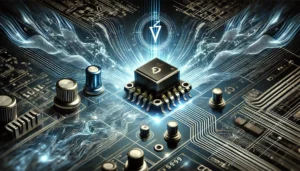