What is Industrial Automation:
Automation can be defined as the technology by which a process or procedure is accomplished without human assistance. It is implemented using a program of instructions combined with a control system that executes the instruction To automate a process, power is required, both to drive the process itself and to operate the program and control system Although automation can be applied in a wide variety of areas, it is most closely associated with the manufacturing industries.it was in the context of manufacturing that the term was originally coined by an engineering manager at Ford Motor Company in 1946 to describe the variety of automatic transfer devices and feed mechanisms that had been installed in Ford’s production plants . It is ironic that nearly all modern applications of automation are controlled by computer technologies that were not available in 1946.
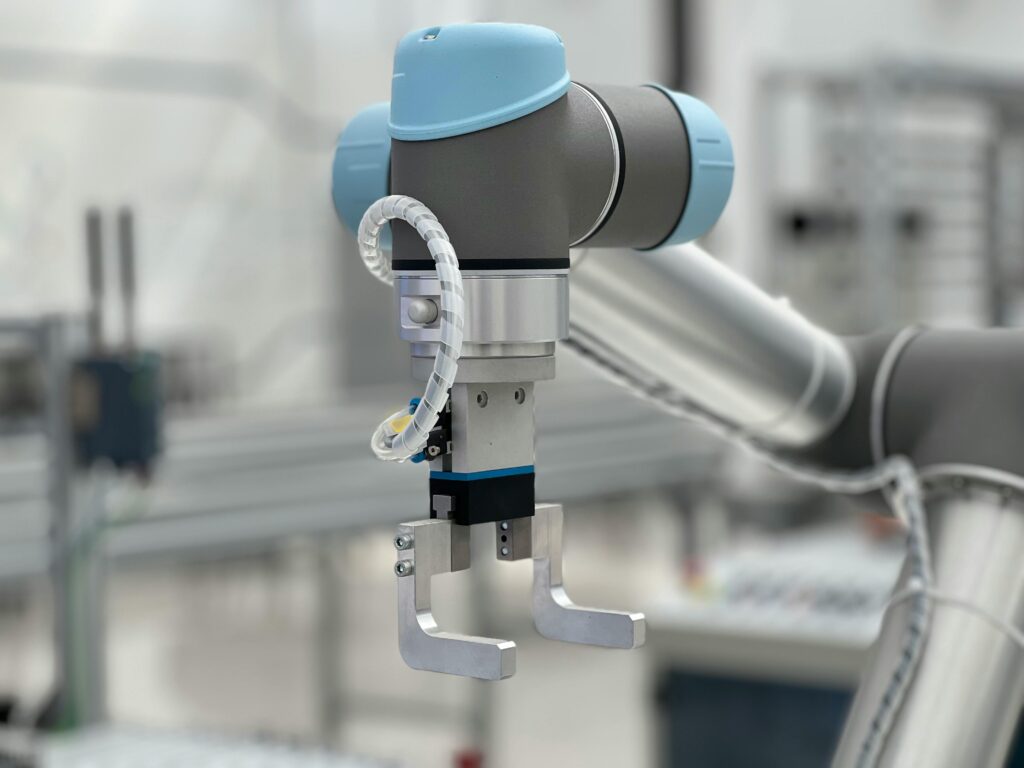
Reason for Automating :
1)To increase labor productivity: Automating a manufacturing operation usually increases production rate and labor productivity. This means greater output per hour of labor input.
2. To reduce labor cost: Ever-increasing labor cost has been and continues to be the trend in the world’s industrialized societies. Consequently, higher investment in automation has become economically justifiable to replace manual operations. Machines are increasingly being substituted for human labor to reduce unit product cost.
3. To mitigate the effects of labor shortages: There is a general shortage of labor in many advanced nations, and this has stimulated the development of automated operations as a substitute for labor.
4. To reduce or routine manual and clerical tasks: An argument can be put forth that there is social value in automating operations that are routine, boring, fatiguing, and possibly irksome. Automating such tasks improves the general level of working conditions.
5. improve worker safety: Automating a given operation and transferring the worker from active participation in the process to a monitoring role, or removing the worker from the operation altogether, makes the work safer. The safety and physical well being of the worker has become a national objective with the enactment of the Occupational Safety and Health Act (OSHA) in 1970. This has provided an impetus for automation.
6. To improve product quality: Automation not only results in higher production rates than manual operation, it also performs the manufacturing process with greater uniformity and conformity to quality specifications.
8)To accomplish process that cannot be done manually: Certain operations cannot be accomplished without the aid of a machine. These processes require precision, miniaturization, or complexity of geometry that cannot be achieved manually. Examples include certain integrated circuit fabrication operations, rapid prototyping processes based on computer graphics (CAD) models, and the machining of complex, mathematically defined surfaces using computer numerical control. These processes can only be realized by computer controlled systems.
9. To avoid the high cost of not automating: There is a significant competitive advantage gained in automating a manufacturing plant. The advantage cannot easily be demonstrated on a company’s project authorization form. The benefits of automation often show up in unexpected and intangible ways, such as in improved quality, higher sales, better labor relations, and better company image. Companies that do not automate are likely to find themselves at a competitive disadvantage with their customers, their employees, and the general public.
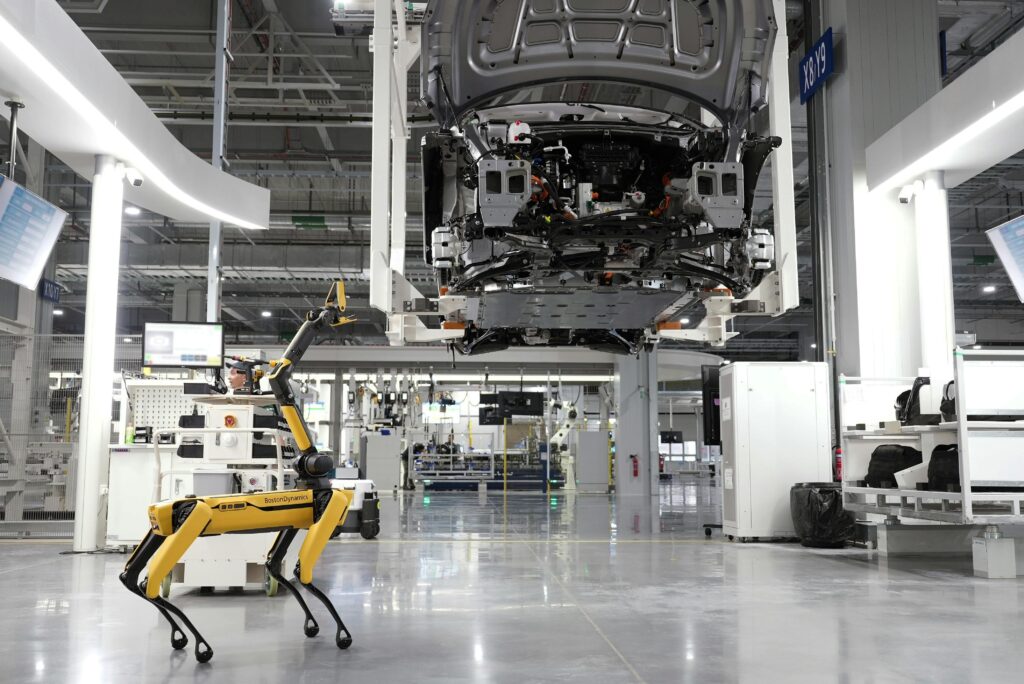
Industrial Automation Type :
Fixed Automation: Fixed automation is a system in which the sequence of processing (or assembly) operations is fixed by the equipment configuration. Each operation dothing (quence is usually simple, involving perhaps a plain linear or rotational motion or an uncomplicated combination of the two, such as the feeding of a rotating spindle. It is the integration and coordination of many such operations into one piece of equipment the interes the system complex. Typical features of fixed automation are (1) high initial that meet for custom-engineered equipment, (2) high production rates, and (3) relative inflexibility of the equipment to accommodate product variety.
The economic justification for fixed automation is found in products that are produced in very large quantities and at high production rates. The high initial cost of the equipment can be spread over a very large number of units, thus making the unit cost attractive compared with alternative methods of production. Examples of fixed automation include machining transfer lines and automated assembly machines.
Programmable Automation: In programmable automation, the production equipment is designed with the capability to change the sequence of operations to accom modate different product configurations. The operation sequence is controlled by a program, which is a set of instructions coded so that they can be read and interpreted by the system. New programs can be prepared and entered into the equipment to produce new products. Some of the features that characterize programmable automation include (1) high investment in general purpose equipment, (2) lower production rates than fixed automation, (3) flexibility to deal with variations and changes in product configuration, and (4) high suitability for batch production.
Programmable automated production systems are used in low and medium- volume production. The parts or products are typically made in batches. To produce each new batch of a different product, the system must be reprogrammed with the set
of machine instructions that correspond to the new product. The physical setup of the machine must also be changed: Tools must be loaded, fixtures must be attached to the machine table, and the required machine settings must be entered. This changeover procedure time. Consequently, the typical cycle for a given product includes a period during which the setup and reprogramming takes place, followed by a period in which the parts in the batch are produced. Examples of programmable automation include numerically controlled (NC) machine tools, industrial robots. and logic controllers.
Flexible Automation: Flexible automation is an extension of programmable automation. A flexible automated system is capable of producing a variety of parts (or products) with virtually no time lost for changeovers from one part style to the next. There is no lost production time while reprogramming the system and altering the physical setup (tooling, fixtures, machine settings). Accordingly, the system can produce various mixes and schedules of parts or products instead of requiring that they be made in batches. What makes flexible automation possible is that the differences between parts processed by the system are not significant, so the amount of changeover required between styles is minimal. The features of flexible automation include (1) high investment for a custom-engineered system, (2) continuous production of variable mixtures of products, (3) medium production rates, and (4) flexibility to deal with product design variations. Examples of flexible automation are the flexible manufacturing systems for performing machining operations. The first of these systems was installed in the late 1960s.
Production Rate:
1)programmable Automation: Low production quantities in the range 1 to 100.
2)Flexible Automation: Medium production quantities in the range of 100 to 10,000 units .
3)Fixed Automation: High production production quantities are 10,000 to millions of units.
Industrial Automation main Components:
1. Control Systems:
Industrial automation uses control systems to manage specific tasks in industries, reducing the need for manual labor. These systems involve hardware and software to control electronic devices or mechanical processes.
2)Programmable Logic Controllers: (PLCs): PLCs are industrial computers, designed to control machinery like factory equipment. They receive input from sensors and send commands based on predetermined conditions to actuators.
3)Distributed Control Systems (DCS): Extended processes often use DCS, where multiple controllers communicate and work together. Control hardware is distributed throughout the plant, while central monitoring software interfaces everything to human-machine interfaces or other input/output devices.
4). Sensors and Actuators:
Looking at the IoT space, sensors become the eyes and ears of these automation systems. They analyze data on a variety of parameters from temperature to pressure and speed.
Types of Sensors:
1) Temperature sensors
2) Proximity sensors
3) Pressure sensors. and more available as your application.
And actuators for executing a command by moving or controlling some mechanism.
3. Robotics:
An industrial robot is a type of programmable machine built to perform different complex tasks with good precision and speed. They are ideal for applications such as assembly, welding, painting and packaging
Types of industrial robots:
Articulated robots
SCARA robots
Delta robots
Collaborative robots (cobots).
4) Human-Machine Interfaces (HMI):
HMIs as the central interface between operators and the automation systems. These interfaces provide graphical representations of processes which can be monitored and manipulated in real-time.
5)Industrial Internet of Things (IoT-Industrial):
The Iot establishes communication between the machines, devices, and systems in industrial settings, ensuring the efficient exchange of data and information. This leads to better decision making and the general efficiency of operations across the organization.
Benefits of IoT:
* Predictive maintenance
* Instant monitoring
* Energy management
* Supply chain improvement
6)AI & Machine Learning:
Artificial Intelligence and Machine learning are widely implemented in the context of industrial automation systems that make them more intelligent and responsive. These technologies provide:
1) Identification of patterns in production data
2)Improvements of manufacturing techniques
3) Quality control and defect detection
4)Predictive maintenance scheduling