Introduction:
A wide variety of sensors are available for collecting data from the manufacturing process for use in feedback control. A sensor is a transducer, which is a device that converts a physical variable of one form into another form that is more useful for the given application. In particular, a sensor is a device that converts a physical stimulus or variable of interest (such as temperature, force, pressure, or displacement) into a more convenient form (usually an electrical quantity such as voltage) for the purpose of measuring the stimulus. The conversion process quantifies the variable, so that it can be interpreted as a numerical value.
sensors are also classified as analog or discrete. An analog sensor produces a continuous analog signal such as electrical voltage, whose value varies in an analogous manner with the variable being measured. Examples are thermocouples, strain gages, and potentiometers. A discrete sensor produces an output that can have only certain values. Discrete sensors are often divided into two categories: binary and digital. A binary sensor produces an on/off signal. The most common devices operate by closing an electrical contact from a normally open position. Limit switches operate in this manner. Other binary sensors include photoelectric sensors and proximity switches.
What is sensor:
A sensor is a device that measures a physical quantity and converts it into a signal which can be read by an observer or by an instrument. Sensors are used in everyday objects such as touch- sensitive elevator buttons (tactile sensor) and lamps which dim or brighten by touching the base. Applications include automation, iot, cars, machines, aerospace, medicine, manufacturing and robotics.
Active And Passive Sensor:
An active sensor responds to the stimulus without the need for any external power. An example is a thermocouple, which responds to an increase in temperature by generating a small voltage (millivolt range) that is functionally related to temperature (in the ideal, its voltage is directly proportional to temperature).
A passive sensor requires an external source of power in order to operate. A thermistor illustrates this case. It also measures temperature, but its operation requires an electric current to be passed through it. As the temperature increases, the thermistor’s electrical resistance is altered. The resistance can be measured and related back to temperature.
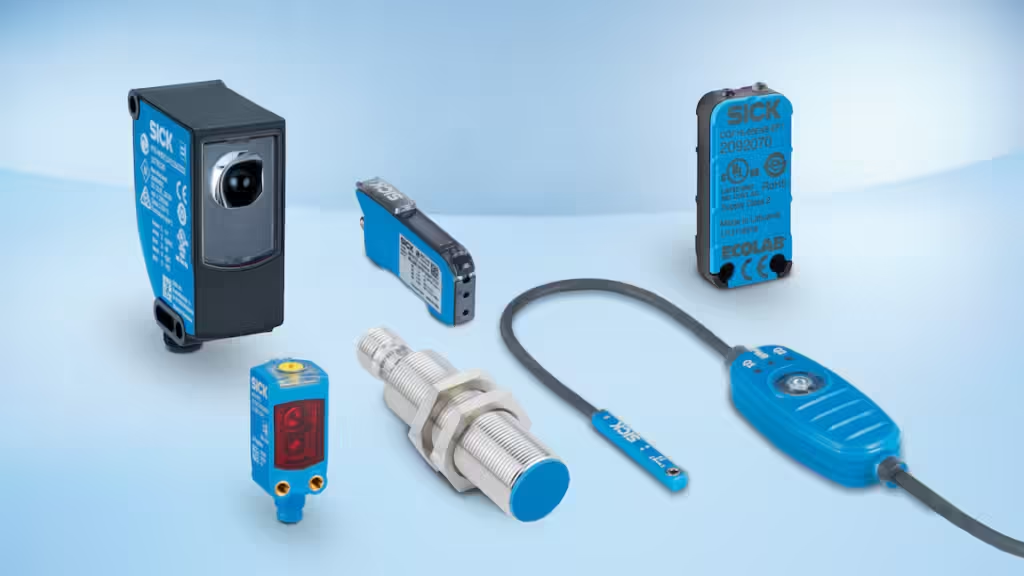
Analog And Digital Sensor:
An analog sensor produces a continuous analog signal such as Temperature sensors, Pressure sensors, Light-dependent resistors (LDR). the analog sensor mostly used in process industry such as food industry. A digital sensor produces an output that can have only two certain values 0 and 1. Examples of Digital Sensors: Proximity sensors, Limit switches, Digital temperature sensors
Characteristic | Analog Sensors | Digital Sensors |
Output Signal | Continuous signal (voltage/current) | Discrete signal (on/off or 0/1) |
Precision | Provides a range of values | Binary output; detects specific states |
Data Representation | Varies smoothly over a range | Represents data as high/low or 0/1 |
Accuracy | More precise for gradual changes in the variable | Limited to detecting conditions or thresholds |
Complexity of Interface | Often requires analog-to-digital conversion (ADC) | Easier to interface with microcontrollers/PLCs |
Use Cases | Temperature, pressure, light intensity monitoring | Object detection, switch operation, motion sensing |
Types of sensor:
Accelerometer: Analog device used to measure vibration and shock. Can be based on various physical phenomena (e.g., capacitive, piezoresistive, piezoelectric).
Ammeter Bimetallic switch: Analog device that measures the strength of an electrical current. Binary switch that uses a bimetallic coil to open and close electrical contact as a result of temperature change. A bimetallic coil consists of two metal strips of different thermal expansion coefficients bonded together.
Bimetallic thermometer: Analog temperature-measuring device consisting of bimetallic coil that changes shape in response to temperature change. Shape change of coil can be calibrated to indicate temperature.
LM35: is a precession Integrated circuit Temperature sensor, whose output voltage varies, based on the temperature around it. It is a small and cheap IC which can be used to measure temperature anywhere between -55°C to 150°C
Dynamometer: Analog device used to measure force, power, or torque. Can be based on various physical phenomena (e.g., strain gage, piezoelectric effect).
Float transducer: Float attached to lever arm. Pivoting movement of lever arm can be used to measure liquid level in vessel (analog device) or to activate contact switch (binary device).
Fluid flow sensor: Analog measurement of liquid flow rate, usually based on pressure difference between flow in two pipes of different diameter.
Fluid flow switch: Binary switch similar to limit switch but activated by increase in fluid pressure rather than by contacting object.
Limit switch: (mechanical) Binary contact sensor in which lever arm or pushbutton closes (or opens) an electrical contact.
Linear encoder: Digital device used to measure linear position and/or speed using a transducer that reads a stationary linear scale indicating position. Speed can be measured as position divided by time lapse. Transducer technologies include optical, magnetic, and capacitive.
Linear variable differential transformer: Analog position sensor consisting of primary coil opposite two secondary coils separated by a magnetic core. When primary coil is energized, induced voltage in secondary coil is function of core position. Can also be adapted to measure force or pressure.
Manometer: Analog device used to measure pressure of gas or liquid. It is based on comparison of known and unknown pressure forces. A barometer is a specific type of manometer used to measure atmospheric pressure.
Ohmmeter: Analog device that measures electrical resistance.
Photoelectric sensor: array Digital sensor consisting of linear series of photoelectric switches. Array is designed to indicate height or size of object interrupting some but not all of the light beams.
Photoelectric switch: Binary noncontact sensor (switch) consisting of emitter (light source) and receiver (photocell) triggered by interruption of light beam. Two common types are: (1) transmitted type, in which object blocks light beam between emitter and receiver; and (2) retroreflective type, in which emitter and receiver are
located in one device and beam is reflected off remote reflector except when object breaks the reflected light beam.
Photometer: Analog sensor that measures illumination and light intensity. Can be based on various photodetector devices, including photodiodes, phototransistors, and photoresistors.
Piezoelectric transducer: Analog device based on piezoelectric effect of certain materials (e.g., quartz) in which an electrical charge is produced when the material is deformed. Charge can be measured and is proportional to deformation. Can be used to measure force, pressure, and acceleration.
Potentiometer: Analog position sensor consisting of resistor and contact slider. Position of slider on resistor determines measured resistance. Available for both linear and rotational (angular) measurements.
Proximity: switch Binary noncontact sensor is triggered when nearby object induces changes in electromagnetic field. Can be based on any of several physical principles, including inductance, capacitance, ultrasonics, and optics.
Radiation pyrometer: Analog temperature-measuring device that senses electromagnetic radiation
in the visible and infrared range of spectrum.
Rotary encoder: Digital device used to measure angular position and/or speed, using a transducer that converts location on a circular scale into rotational position. Rotational speed can be measured as position divided by time lapse. Transducer technologies include optical, magnetic, and capacitive.
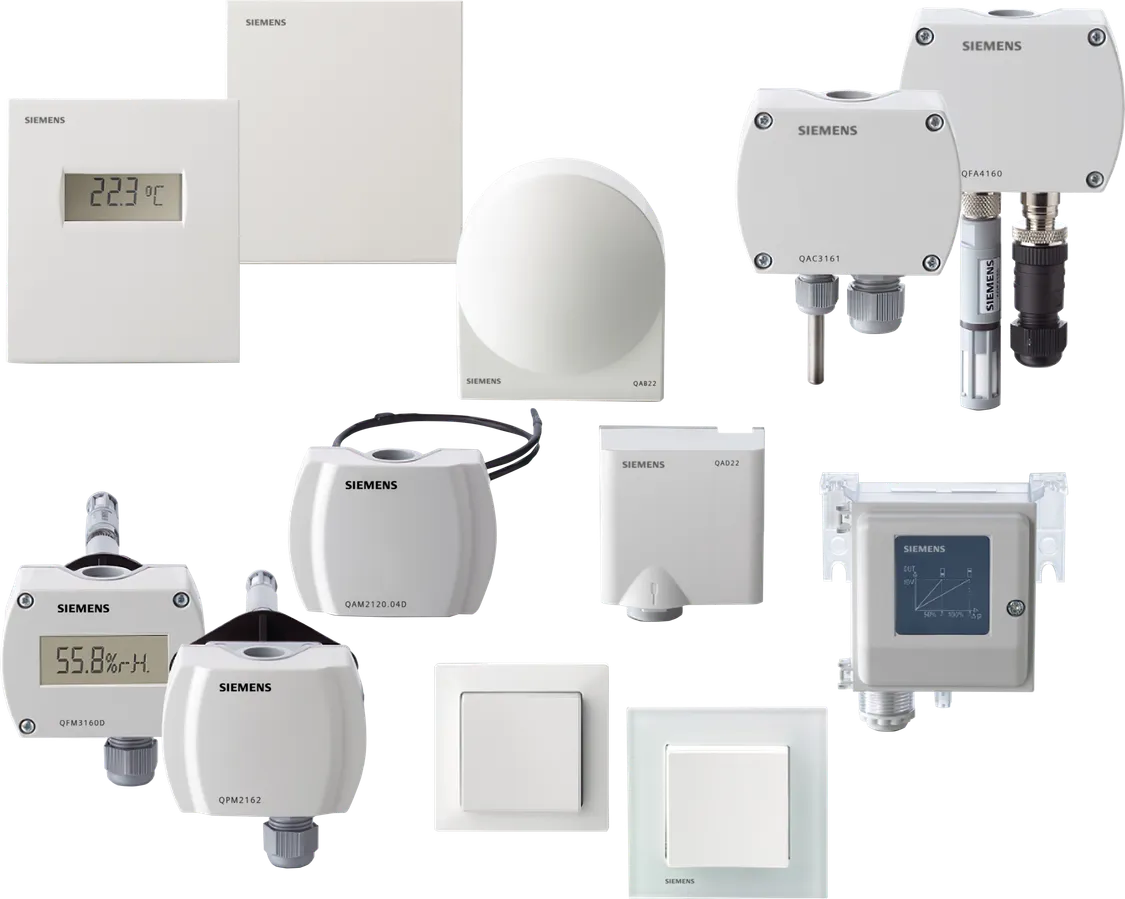
How to select sensor:
- There are certain features which have to be considered when we choose a sensor. They are as given below:
- 1. Accuracy
- 2. Environmental condition – usually has limits for temperature/ humidity
- 3. Range – Measurement limit of sensor
- 4. Calibration – Essential for most of the measuring devices as the readings changes with time
- 5. Resolution – Smallest increment detected by the sensor
- 6. Cost
- 7. Repeatability – The reading that varies is repeatedly measured under the same environment
Why Are Sensors Important in Industrial Automation?
Increased efficiency: with continuous system monitoring Sensors will increase efficiency and reduce energy consumption.
Safety: Sensors can detect dangerous conditions (such as overpressure or overheating) and signal an alarm or shut down the unit to prevent accidents.
Quality control: Sensors help maintain production consistency by ensuring that variables such as temperature and pressure remain within specified limits.
Cost Savings: Early Problem Detection Through sensors, expensive downtime and equipment damage can be prevented.